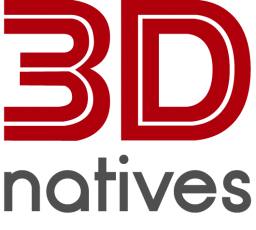
Od začetka leta britanski proizvajalec Rolls-Royce, hčerinska družba BMW Group, 3D-tiska plastične in kovinske dele za svoj model Rolls-Royce Ghost. Deli so izdelani vzdolž proizvodne linije na različnih lokacijah v svetovni proizvodni mreži in so sestavljeni v Goodwoodu v Angliji. Proizvajalec pravi, da bo v Rolls-Royce Ghost v življenjskem ciklu modela avtomobila vgradil več sto tisoč 3D-natisnjenih delov, pri čemer se bo oprl na izkušnje BMW-ja z novim centrom za aditivno proizvodnjo. Skupina se želi zanašati na tehnologije 3D-tiska za izdelavo serijskih vozil, Rolls-Royce pa je le začetek te velike dogodivščine.
Junija lani je BMW Group v Oberschleissheimu, severno od Münchna, odprl svoj kampus za aditivno proizvodnjo, da bi združil približno 50 rešitev 3d-tiska plastike in kovine. Cilj skupine je industrializirati te proizvodne procese, jih avtomatizirati in nenehno oblikovati. Daniel Schäfer, vodja integracije proizvodnje in integracije pilotnih obratov pri BMW Group, dodaja: »Procesi, kot je aditivna proizvodnja, nam pomagajo skrajšati razvojne cikle in s tem
našim vozilom hitreje do proizvodnje. 3D-tisk nam pomaga tudi pri zmanjševanju časa izdelave komponent, hkrati pa ohranja visoke standarde kakovosti. ” Te prednosti je hitro vključila angleška podružnica skupine Rolls-Royce, ki je lahko implementirala 3D-tisk in zdaj končne dele oblikuje v večjih količinah. Še vedno smo daleč od množične proizvodnje, vendar je ta razvoj vseeno spodbuden.
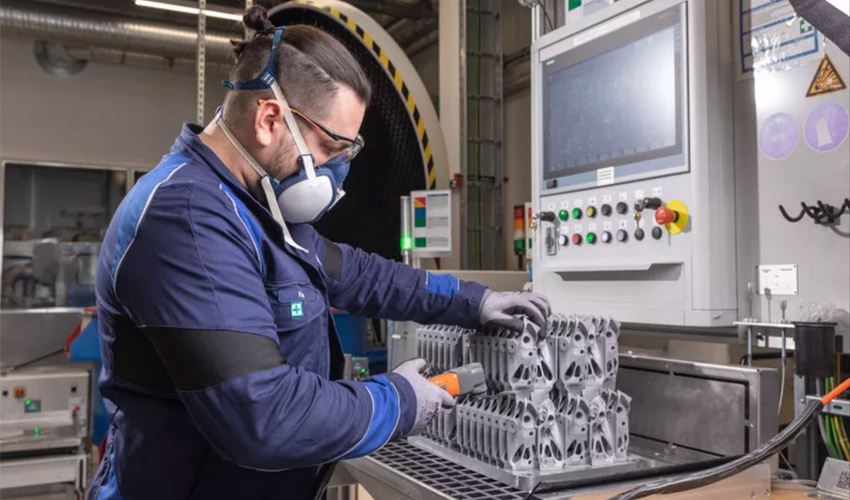
Rolls-Royce se zanaša na plastične in kovinske tehnologije
Lani oktobra je Rolls-Royce v svojem modelu Extended Ghost predstavil 3D-natisnjene komponente. Deli, ki jih je natisnil proizvajalec, so namenjeni potniški celici in delom pod karoserijo ter so zelo funkcionalni in togi. Za notranjost je skupina oblikovala plastične sestavne dele z uporabo selektivnega laserskega sintranja (SLS) in Multi Jet Fusion tehnologijo, medtem ko je bila za kovinske dele prednostna tehnika “Powder Bed Fusion” (PBF). Slednje izdelujejo v tovarni BMW Group v nemškem Landshutu, nato pa jih skoraj popolnoma samodejno vključijo v proizvodni proces.
Vsak 3D-natisnjen kovinski del ima edinstveno QR kodo in identifikacijske številke. Ekipe z bolj tradicionalnimi postopki izdelave, verjetno ne bi mogle prilagoditi vsakega dela s temi podrobnostmi. Upoštevajte tudi, da je logotip britanske blagovne znamke prisoten na vseh komponentah.
Pri oblikovanju so se ekipe BMW in Rolls-Royce zanašale na generativni dizajn, da bi optimizirale strukturo vsake komponente in ponudile lažji in učinkovitejši del. Pojasnjujejo: »V zgodnjih fazah razvoja novega Rolls-Royce Ghost so inženirji analizirali na stotine komponent in preizkusili, v kolikšni meri je bila možna proizvodnja z uporabo aditivnih proizvodnih procesov. Poudarek je bil na prednostih glede teže in geometrije v primerjavi s tradicionalnimi postopki in ekonomskih koristih. Z izbiro primernih komponent za serijsko izdelavo s 3D-tiskom so strokovnjaki opredelili merila in zahteve za 3D-natisnjene komponente in jih s pomočjo strokovnjakov za obdelavo podatkov prevedli v “strojni jezik”. To je pomenilo začetek novega sistema umetne inteligence, ki BMW Group omogoča hitrejše in zgodnejše prepoznavanje potencialnih 3D tiskanih komponent v prihodnjih vozilih. “
Cilj je čim bolj industrializirati proizvodni postopek, od zasnove do izdelave, in postopoma povečati število 3D-natisnjenih delov. Zagotovo pa bi vse to moralo spremeniti odprtje tega namenskega centra v Nemčiji
Kaj menite o Rolls Royce integraciji aditivne proizvodnje?
Vir: 3dnatives.com.