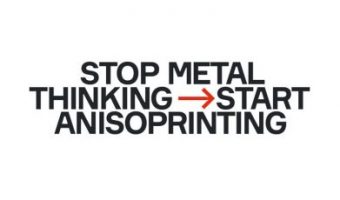
Anisoprint je tehnologija za proizvodnjo optimalnih kompozitov s 3D-tiskom neprekinjenih vlaken. Ustvarite lahko kakršne koli oblike, brez orodij, modelov, strojne ali naknadne obdelave.
Takšni deli so lahko:
– 30 x močnejši od plastike,
– 7 x lažji od jekla,
– 2 x močnejši in lažji, kot aluminij.
3D-tisk z neprekinjenimi vlakni
Vse tehnologije za 3D-tisk z neprekinjenimi vlakni lahko razdelimo v dve skupini; tehnologije prepreg in tehnologije ko-ekstrudiranja. Razlika med njimi je v trenutku v katerem se ustvari kompozitni material ali ko se združijo ojačitvena vlakna in material uporabljen, kot matrica. To je lahko pred ali med postopkom 3D-tiska.
Prepared tehnologija: suha vlakna se združijo z drugim polimerom v ločenem postopku; takšen material imenujemo prepreg. Prepreg je lahko v obliki filamenta ali traku. Postopek tiska sestavljata taljenje polimera s prepreg-om in nanašanje tega, plast za plastjo, na del. Taljenje omogoča, da se vlakna povežejo.
Postopek ko-ekstrudiranja: suha vlakna se ekstrudirajo skupaj s polimerom med samim postopkom 3D-tiska in kompozitni material je ustvarjen “in situ”.
Prednosti in pomankljivosti
Oba postopka imata svoje prednosti in slabosti.
Prepreg:
+ Odlična impregnacija in adhezija.
– Omejene oblike.
– Konstantno razmerje volumna vlaken.
– Predhodno definiran matrični material.
Ko-ekstruzija:
+ Kompleksne oblike.
+Fleksibilno razmerje volumna vlaken.
+ Širok spekter matričnih materialov.
– Slaba impregnacija in adhezija.
Tako lahko z uporabo prepreg tehnologije dobimo material odlične kakovosti, ko-ekstruzija pa nam ponuja več svobode pri oblikovanju in lastnostih.
Ko-ekstruzija kompozitnih vlaken
Dobra novice, izkoristite lahko prednosti obeh tehnologij, brez kompromisov. Anisoprint je razvil tehnologijo ko-ekstruzije kompozitnih vlaken (CFC).
Najprej pojasnimo, kaj so kompozitna vlakna. To so suha vlakna predhodno impregnirana s posebno polimerno mešanico in nato sušena. Rezultat tega so toga vlakna, ki jih imenujemo kompozitna vlakna, saj že z impregnacijo postanejo kompoziti. Material nato uporabimo za ojačanje plastike med postopkom 3D-tiska. Med tiskom se kompozitna vlakna ko-ekstrudirajo skupaj s plastiko in ustvarijo bi-matrični kompozitni del. Kompozitni ekstruder ima dve vhodni in eno izhodno enoto. Ena vhodna enota je namenjena kompozitnim vlakom in druga plastičnemu filamentu. Takšen proces omogoča pridobivanje ojačanih delov visoke kakovosti, skupaj s svobodo pri oblikovanju in matričnih materialih.
Kompozitna vlakna
Predhodna impregnacija vlaken s polimerno mešanic , v ločenem postopku, nam pomaga doseči izjemno kakovost materialov, brez razpok, kar je ključnega pomena za zmogljivost materiala. Zahvaljujoče ko-ekstruziji lahko ustvarite dele kompleksnih oblik in smeri vlaken ukrivljenih trajektorij.
Ločeno dovajanje ojačitvenega materiala in plastike omogoča izbiro katerega koli materiala, kot matrice, za pridobivanje kompozitnih delov z določenimi lastnostmi (temperaturna in svetlobna odpornost, odpornost na kemikalije in vlago).
Rešetkaste structure
Najbolj pomembna prednost, ki jo omogoča ko-ekstruzija je fleksibilno razmerje volumna vlaken, saj omogoča ustvarjanje rešetkastih struktur, najbolj učinkovitih struktur za kompozitne materiale.
Kompozitni materiali imajo usmerjene lastnosti, kar pomeni, da sta njihova moč in togost vzporedni s smerjo vlaken. Rešetkaste strukture sestavljajo enodimenzionalne rešetke, zato se teža vedno porazdeli med vlakni. Zaradi tega so rešetkaste strukture najboljša izbira za kompozite.
Tehnologija Anisoprint je edini način za ustvarjanje kompozitnih rešetkastih struktur, saj edina omogoča raznoliko količino materiala v križiščih rešetk. Kadar je volumen materiala konstanten, dobite strukturo s podvojenim volumnom materiala v križiščih. Takšne strukture srečamo v naravi in proizvodnji; na primer Vickers Wellington, bombno letalo uporabljeno v 2. Svetovni vojni, je zahvaljujoč rešetkasti oklepni strukturi, deloval tudi, če je bil resnejše poškodovan. Če se je poškodovala ena od rešetk, so njeno nosilnost prevzele preostale in struktura je ostala funkcionalna.
Uporaba kompozitnih rešetkastih polnil omogoča pridobivanje izjemno trdnih delov in istočasno z manjšo težo. Kot vidite na posnetku, že 30 % polnilo zagotavlja 350 % moči, med tem, ko 100 % plastično polnilo ponuja le 1/3 moči.
Izbirate lahko med štirimi vrstami polnil z ojačanimi vlakni: trdnimi, rombičnnimi, isogridnimi in anisogridnimi.
Vir: Anisoprint.com